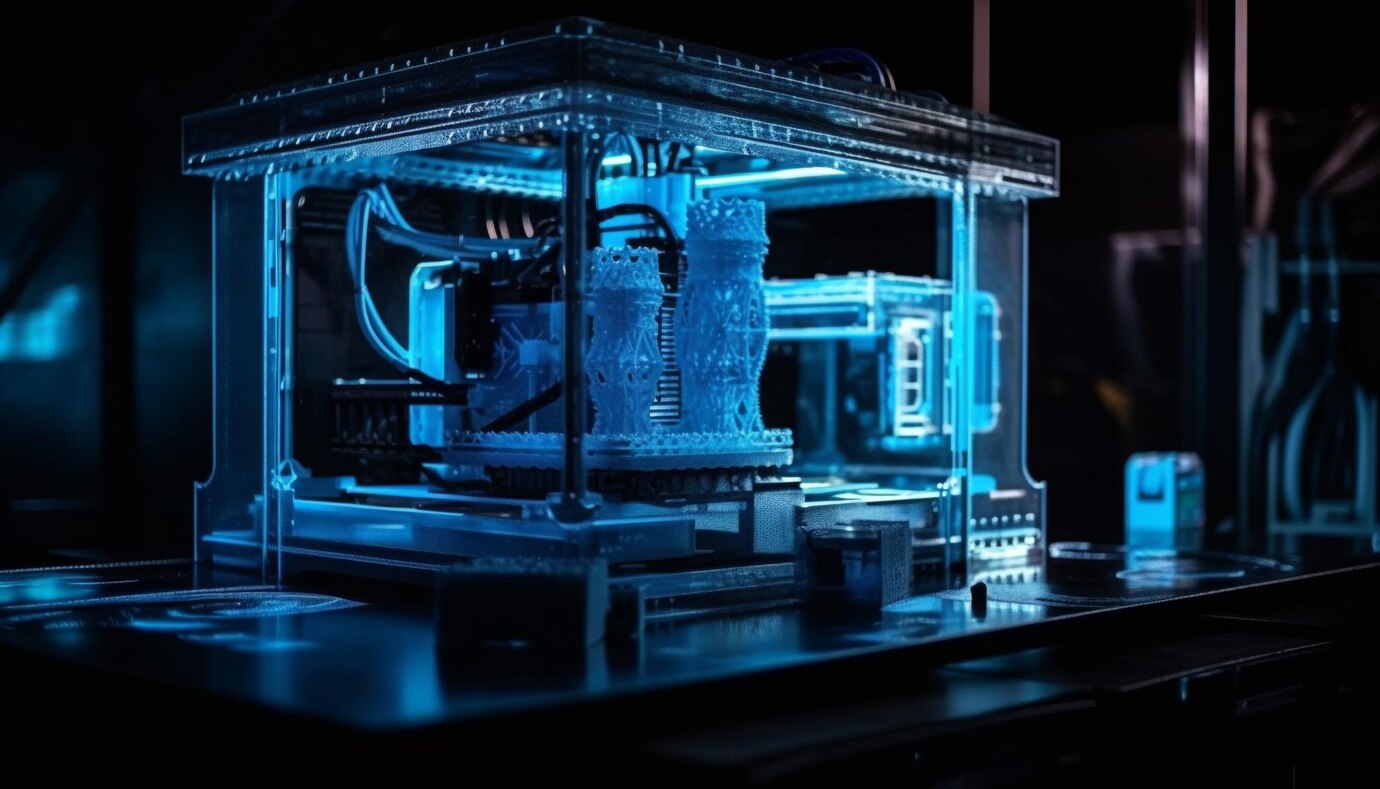
Revolutionizing the Aerospace Industry with 3D Printing
The Aerospace industry has always been at the forefront of technological innovation, pushing the boundaries of what’s possible to explore realms beyond our immediate reach. In recent years, an exciting facet of technology has been making a significant impact on this industry: 3D printing. Let’s delve into how 3D printing is revolutionizing aerospace, sending ripples of change through this high-flying sector.
Lighter and Stronger Components:
One of the greatest benefits 3D printing has bestowed upon the aerospace industry is the manufacturing of lighter yet stronger components. The traditional manufacturing process involves creating large pieces and whittling them down to the needed part, often resulting in waste and a potential loss of structural integrity. In contrast, 3D printing builds components layer-by-layer from the ground up, making it possible to design parts with intricate internal geometries that reduce weight while maintaining, or even augmenting strength.
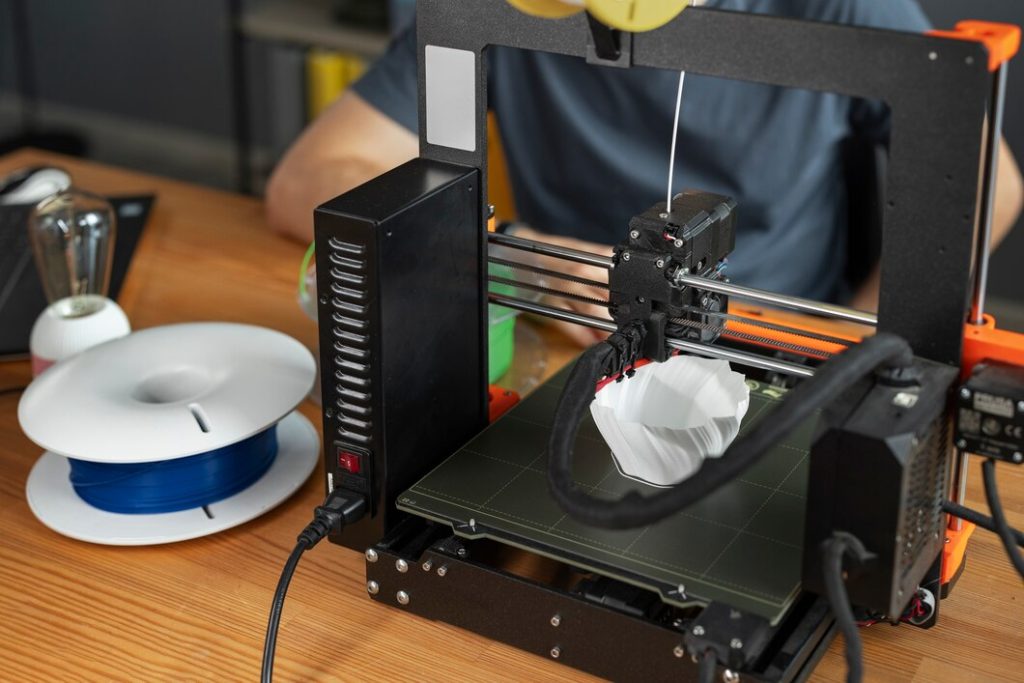
Sustainable Manufacturing:
Aerospace manufacturing often requires specific and rare materials that can stand up to the harsh conditions of space. 3D printing can utilize aerospace-grade materials like titanium and Inconel ensuring components stand up to rigorous demands while reducing waste in the manufacturing process. By minimizing the need for excess materials and reducing waste, 3D printing offers a more sustainable approach to aerospace manufacturing.
Reduced Time to Market:
In the aerospace industry, time is always of the essence. Developing a new aircraft or spacecraft is a time-consuming process that undergoes rigorous testing and multiple iterations. Traditional methods often involve lengthy manufacturing times for prototypes and components. 3D printing can significantly shorten these timelines by swiftly creating complex prototypes and parts on-demand, thereby reducing the time from concept to launch.
Customization and Flexibility:
Every space mission has unique needs, requiring purpose-specific equipment and components. 3D printing provides the flexibility to create custom parts tailored to specific mission requirements without the need for extensive manufacturing modifications. This is particularly valuable in the creation of spacecraft where off-the-shelf components may not meet the unique requirements of certain missions.
On-Board Printing and Repairs:
One of the most exciting potentials for 3D printing in aerospace lies in the ability to conduct on-board printing and repairs. The concept of manufacturing necessary parts in-flight or during a space mission can be a game-changer to ensure the sustainability of long-term missions. Astronauts could potentially use 3D printing to replace parts or equipment that become damaged or depleted during missions, even possibly using raw materials available on other planets to create necessary supplies.
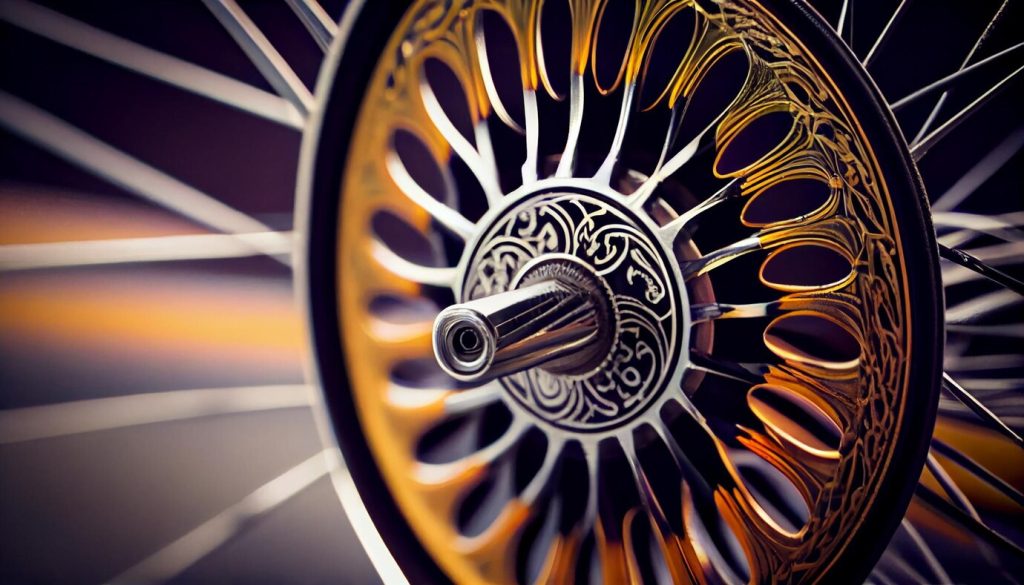
Creation of Nano-Satellites:
The advent of small, lightweight, and cost-effective satellites, commonly known as Nano-Satellites, owes a large part of its success to 3D printing. The technology’s capability to create compact and lightweight components has made it possible to manufacture these small yet powerful satellites. As a result, space exploration and studies have become more accessible to various sectors, including academia and private companies.
In the coming years, the influence of 3D printing in aerospace is undoubtedly going to grow. The dawning of this technology promises to shape a brave new world in aerospace manufacturing and design. It’s an exhilarating time as we watch the boundaries between science fiction and reality blur, where the depths of the universe are slowly but surely becoming reachable, thanks in part to the impact of 3D printing technology. As we continue to unravel the full potential of additive manufacturing, one cannot help but wonder: the sky is no longer the limit, but just the beginning.