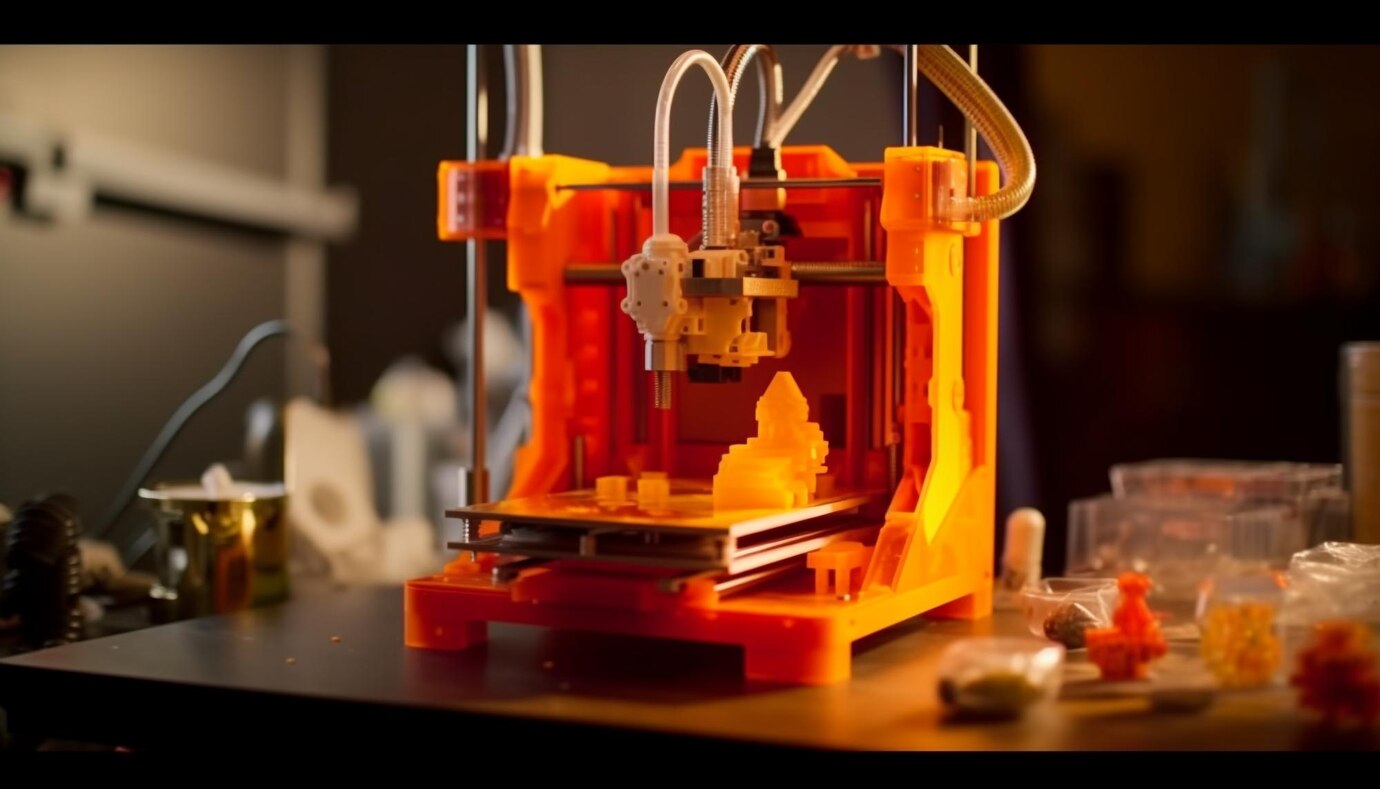
How to Solve the Most Common 3D Printing Issues
As 3D printing continues to revolutionize numerous sectors, from healthcare to manufacturing and beyond, users must be equipped to troubleshoot common problems to ensure peak printer performance. Here, we delve into some of the primary issues presented by 3D printing along with their solutions to help you fully harness the incredible potential of this innovation.
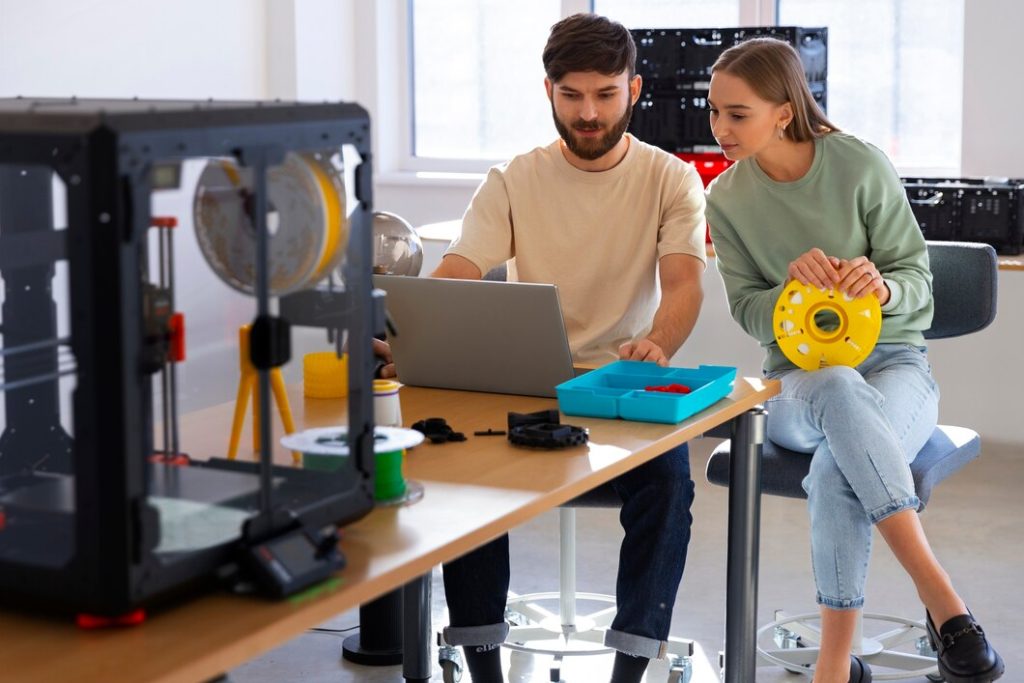
Warped Prints:
Perhaps the most widespread complaint in 3D printing is warping, where the edges of an object curl up and away from the print bed. This is mainly due to uneven cooling, causing material shrinkage.
Solution: Ensure an appropriate temperature for the print bed, specific to the material being used. A heated print bed can keep the lower layers of a print warmer for longer, reducing shrinkage risk. Using an adhesive on your printing bed can also help the print stick better, giving it a lesser chance to warp.
Stringing or Oozing:
Residual filament might sometimes be dragged across the print, resulting in thin strings or “blobs” forming on your model. The issue often arises when the nozzle pressure is not properly relieved before making a move to a different section of the print.
Solution: Activating “retraction” in your slicer software can help. This pulls the filament out of the nozzle when the print head needs to move between different areas of your 3D print, reducing the chance of stringing or oozing.
Under-Extrusion:
When insufficient material is deposited, you come across an issue known as under-extrusion, featuring empty spaces within the layers of your printed model or layers not being printed at all.
Solution: Check to see if your filament is tangled or if your extruder is clogged, two of the most common causes for under-extrusion. Increasing extrusion temperature can also help, as filament can flow more freely at higher temperatures.
Poor Bed Adhesion:
A well-leveled print bed is critical for successful 3D printing, and poor bed adhesion could lead to slippage, toppling, or warping of your model.
Solution: Regularly check and adjust your build plate leveling. Also, ensure your bed surface is clean and possibly apply a bed adhesive. The first layer height and speed are also crucial, so consider lowering your initial layer speed and ensuring the first layer height matches the filament diameter.
Over-Extrusion:
Opposite to under-extrusion, over-extrusion happens when too much filament flows out of the nozzle, resulting in bloated and imprecise prints.
Solution: First, ensure the filament diameter in your slicing software matches the filament you’re using in reality. Also, check your extruder’s calibration settings and make sure they’re accurate.
Layer Shifting:
When print layers don’t align perfectly, it leads to an issue called ‘layer shifting’ or ‘layer misalignment.’ It could be triggered due to a range of factors including loose belts, incorrect print speed, or improper lubrication.
Solution: Tighten any loose belts or screws, lower your print speed, or ensure your printer’s moving parts are well lubricated for smooth movement. A comprehensive check of the printer for loose or broken parts could also highlight the problem source.
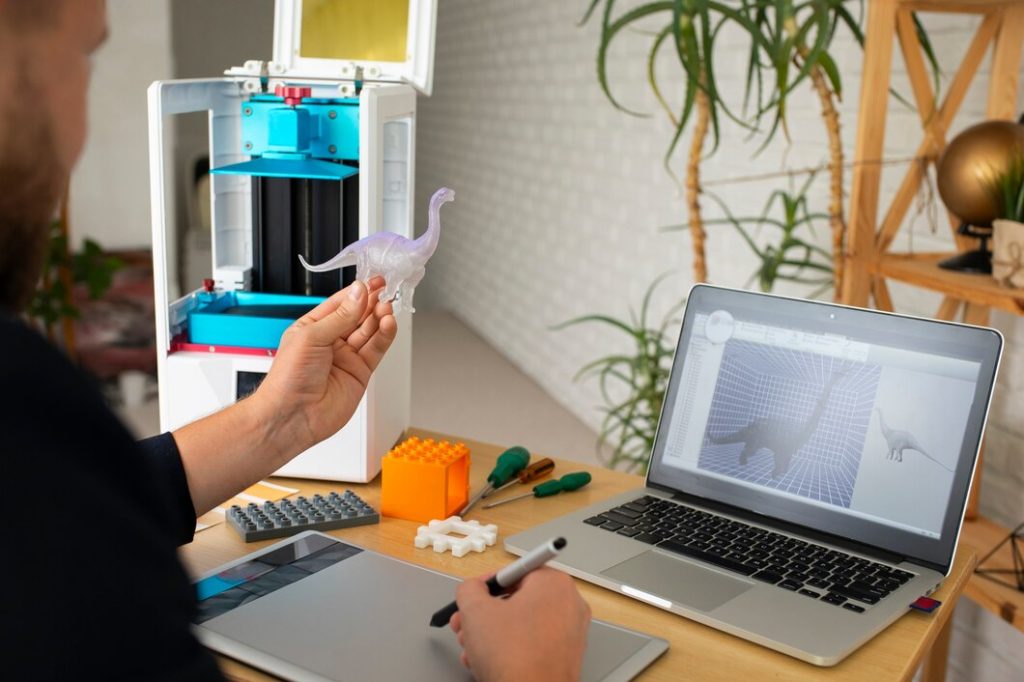
While this guide does address some common 3D printing issues, remember that each printer is unique, and a wide range of variables can affect your print quality. Diligent maintenance, careful calibration, and thorough cleanup practices can go a long way in preventing most issues.
There is no magic solution, quick fix, or one-size-fits-all answer to these problems. Handling 3D printing issues successfully requires patience, a clear understanding of your specific printer, and a good grasp of 3D printing fundamentals. However, by applying these tips, you can significantly augment your 3D printing experience and create exquisite prints with minimal issues.